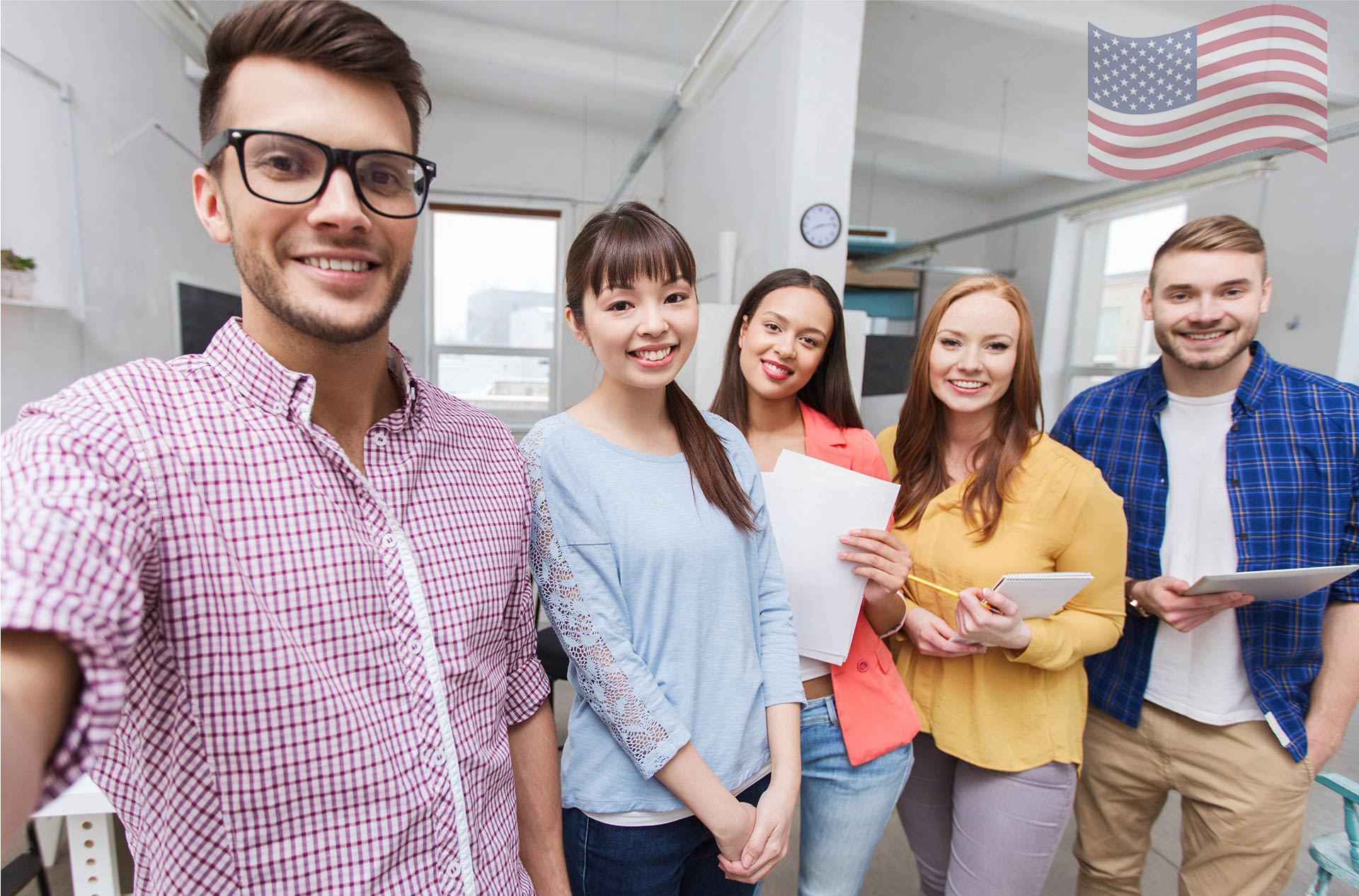
Workplace Health & Safety in the United States
Three Department of Labor (DOL) agencies have responsibility for the administration and enforcement of the laws enacted to protect the safety and health of workers in America.
- Occupational Safety and Health Administration
- OSHA administers the Occupational Safety and Health (OSH) Act.
- Safety and health conditions in most private industries are regulated by OSHA or OSHA-approved state plans.
- Nearly every employee in the nation comes under OSHA’s jurisdiction with some exceptions such as miners, some transportation workers, many public employees, and the self-employed.
- Employers subject to the OSH Act also have a general duty to provide work and a workplace free from recognized, serious hazards.
- OSHA also administers the Whistleblower Protection program, ensuring an employer cannot retaliate by taking “adverse action” against workers who report injuries, safety concerns, or other protected activity.
The Occupational Safety and Health Administration (OSHA) publishes a safety inspection checklist designed to help employers look over their workplaces and make sure they meet OSHA safety requirements. Before getting a safety inspection employers should go over the checklist to make sure they will pass. The checklist covers many standard OSHA regulations that apply to a variety of businesses, such as sanitation requirements, aisleway requirements and record keeping requirements.
Self-Inspection Scope
Your self-inspections should cover safety and health issues in the following areas:
- Processing, Receiving, Shipping and Storage – equipment, job planning, layout, heights, floor loads, projection of materials, material handling and storage methods, training for material handling equipment.
- Building and Grounds Conditions – floors, walls, ceilings, exits, stairs, walkways, ramps, platforms, driveways, aisles.
- Housekeeping Program – waste disposal, tools, objects, materials, leakage and spillage, cleaning methods, schedules, work areas, remote areas, storage areas.
- Electricity – equipment, switches, breakers, fuses, switch-boxes, junctions, special fixtures, circuits, insulation, extensions, tools, motors, grounding, national electric code compliance.
- Lighting – type, intensity, controls, conditions, diffusion, location, glare and shadow control.
- Heating and Ventilation – type, effectiveness, temperature, humidity, controls, natural and artificial ventilation and exhausting.
- Machinery – points of operation, flywheels, gears, shafts, pulleys, key ways, belts, couplings, sprockets, chains, frames, controls, lighting for tools and equipment, brakes, exhausting, feeding, oiling, adjusting, maintenance, lockout/tagout, grounding, work space, location, purchasing standards.
- Personnel – training, including hazard identification training; experience; methods of checking machines before use; type of clothing; PPE; use of guards; tool storage; work practices; methods for cleaning, oiling, or adjusting machinery.
- Hand and Power Tools – purchasing standards, inspection, storage, repair, types, maintenance, grounding, use and handling.
- Chemicals – storage, handling, transportation, spills, disposals, amounts used, labeling, toxicity or other harmful effects, warning signs, supervision, training, protective clothing and equipment, hazard communication requirements.
- Fire Prevention – extinguishers, alarms, sprinklers, smoking rules, exits, personnel assigned, separation of flammable materials and dangerous operations, explosion-proof fixtures in hazardous locations, waste disposal and training of personnel.
- Maintenance – provide regular and preventive maintenance on all equipment used at the worksite, recording all work performed on the machinery and by training personnel on the proper care and servicing of the equipment.
- PPE – type, size, maintenance, repair, age, storage, assignment of responsibility, purchasing methods, standards observed, training in care and use, rules of use, method of assignment.
- Transportation – motor vehicle safety, seat belts, vehicle maintenance, safe driver programs.
- First Aid Program/Supplies – medical care facilities locations, posted emergency phone numbers, accessible first aid kits.
- Evacuation Plan – establish and practice procedures for an emergency evacuation, e.g., fire, chemical/biological incidents, bomb threat; include escape procedures and routes, critical plant operations, employee accounting following an evacuation, rescue and medical duties and ways to report emergencies.
Able Audit comes with over 100 pre-built checklists to help you get started with workplace inspections, or you can use your existing checklists.
Learn more about how Able Audit safety inspection features can you help you perform and manage inspections, distribute reports and manage action items.